I have been asked how I used a standard (9 O'clock fork position) bellhousing with a straight clutch fork in my Malibu. Here is what I did...hope it helps those of you interested out.
I have Heddman Hussler #65219 headers, they are long tube, big pipe diameter (1 7/8").
Other brands or routing styles may not allow this to be done.
I used a Lakewood safety bellhousing
The floor of my old car required a minor amount of clearancing with a rounded wooden driver and a large hammer, where the end of the clutch fork was. This was probably more due to worn out body bushings than a real tight clearance area. If more room were needed I probably would have cut a short length of 1" pipe in half and welded it into the floor.
I also trimmed the fork its self at the top/end to aid clearance. You can see the top edge was ground back to clear the floorboard.
The different height that the straight fork end is at required cutting off the inner arm of the Z bar and relocating it. My Z bar was all reinforced up BEFORE I realized that I needed to cut it. So there is a rectangle area on my Z bar that shows where the arm used to be. I cut the stock inner arm off and flipped it over and mounted it on the other side of the Z bar tube. As hard as these Z bars are to find and as much as people want for these things - I can see being afraid to modify one w/o any exact measurements. It's ok if you want to turn back now.
A stock Z bar and my modified one
More pics from various angles...
Notice the length I had to make my linkage to the fork. It comes about an inch from my header tubes.
Thats all I have to show right now. If I can help make sense of any of this just let me know.
I have Heddman Hussler #65219 headers, they are long tube, big pipe diameter (1 7/8").
Other brands or routing styles may not allow this to be done.
I used a Lakewood safety bellhousing
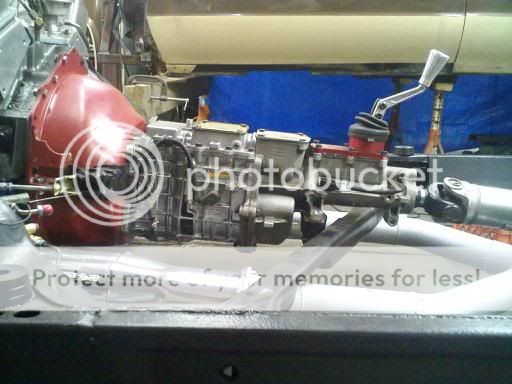
The floor of my old car required a minor amount of clearancing with a rounded wooden driver and a large hammer, where the end of the clutch fork was. This was probably more due to worn out body bushings than a real tight clearance area. If more room were needed I probably would have cut a short length of 1" pipe in half and welded it into the floor.
I also trimmed the fork its self at the top/end to aid clearance. You can see the top edge was ground back to clear the floorboard.
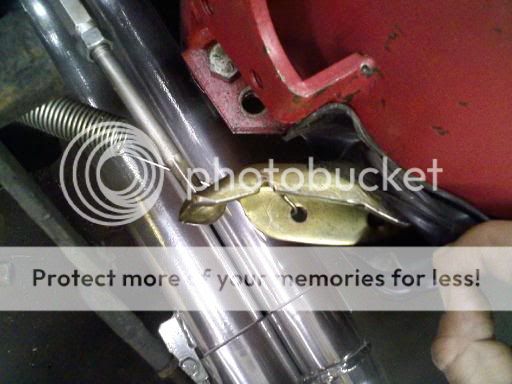
The different height that the straight fork end is at required cutting off the inner arm of the Z bar and relocating it. My Z bar was all reinforced up BEFORE I realized that I needed to cut it. So there is a rectangle area on my Z bar that shows where the arm used to be. I cut the stock inner arm off and flipped it over and mounted it on the other side of the Z bar tube. As hard as these Z bars are to find and as much as people want for these things - I can see being afraid to modify one w/o any exact measurements. It's ok if you want to turn back now.
A stock Z bar and my modified one
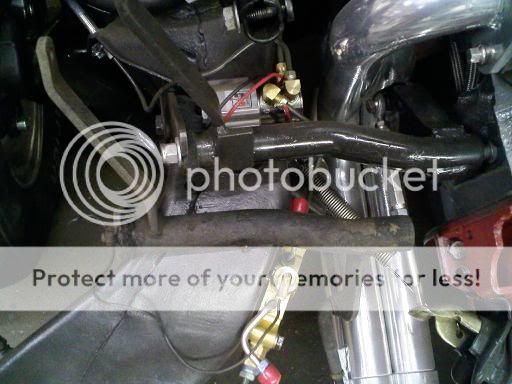
More pics from various angles...
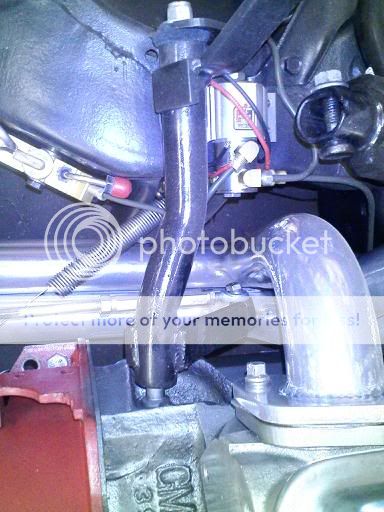
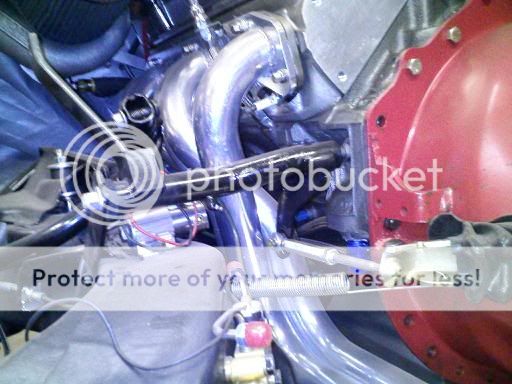
Notice the length I had to make my linkage to the fork. It comes about an inch from my header tubes.
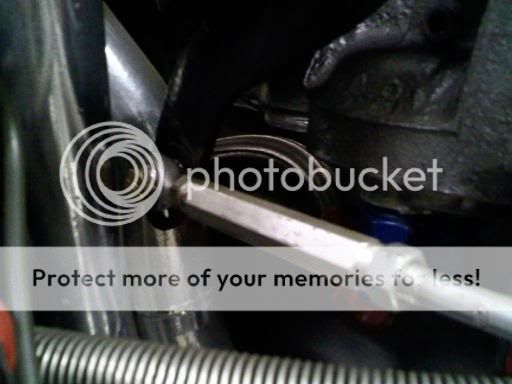

Thats all I have to show right now. If I can help make sense of any of this just let me know.